I made another DVF Julian a few weeks ago and already wore it to work, I was making this pattern for a friend of mine and while I had it out decided to cut one for myself. This fabric is a rayon/lycra print from Emma One Sock, my favorite fabric dealer, er, I mean supplier. :-)
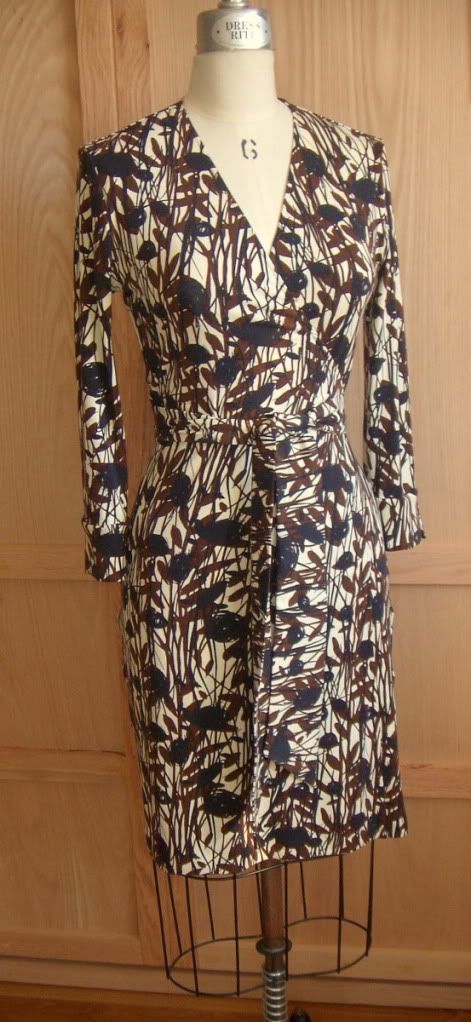
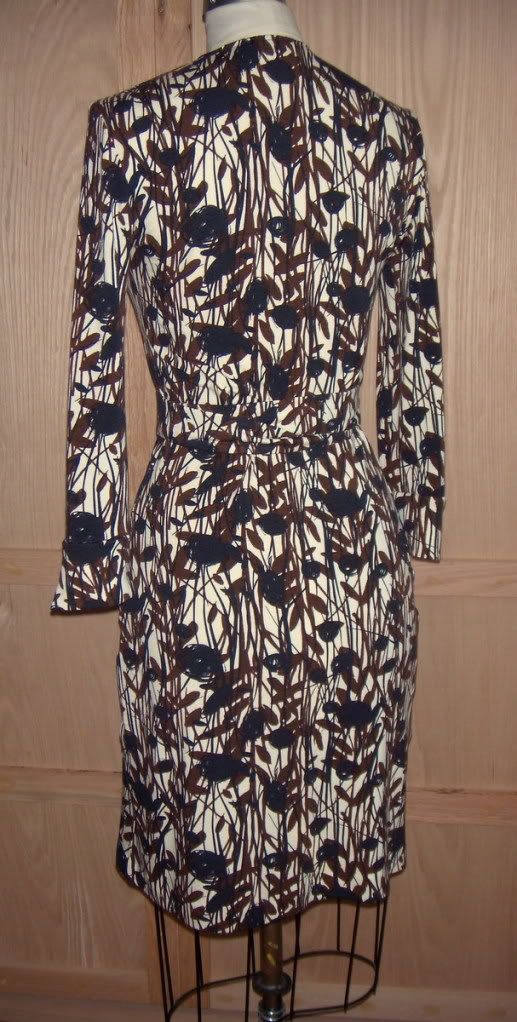
For this fabric I chose to finish the edges by serging 1/4" clear elastic to the neckline and front edges in one pass, then turning to the inside and topstitching. I use a special elasticator foot for my serger, which helps guide the elastic exactly on the seamline and has a tension screw to set how much I want the elastic stretched while it's being serged. Around the neckline I want enough stretch so the fabric puckers a bit when laying flat, when worn wrapped and tied it flattens out and prevents any gaping. When I get to the front edges of the skirt, I undo the tension on the elastic so it doesn't pucker.
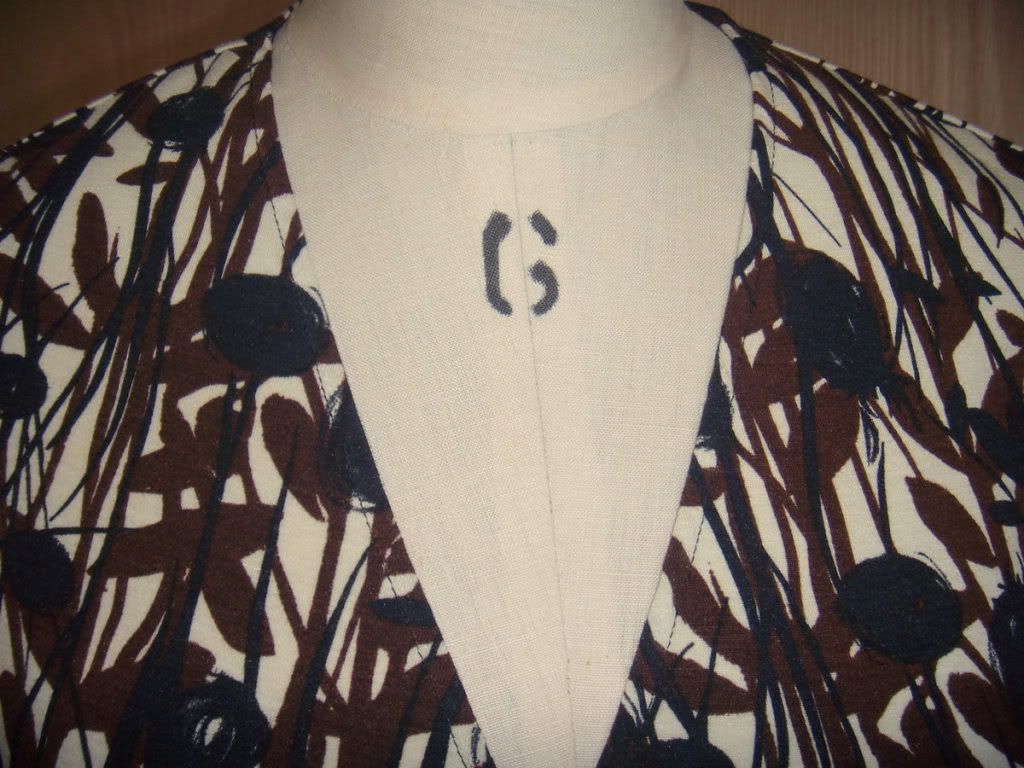
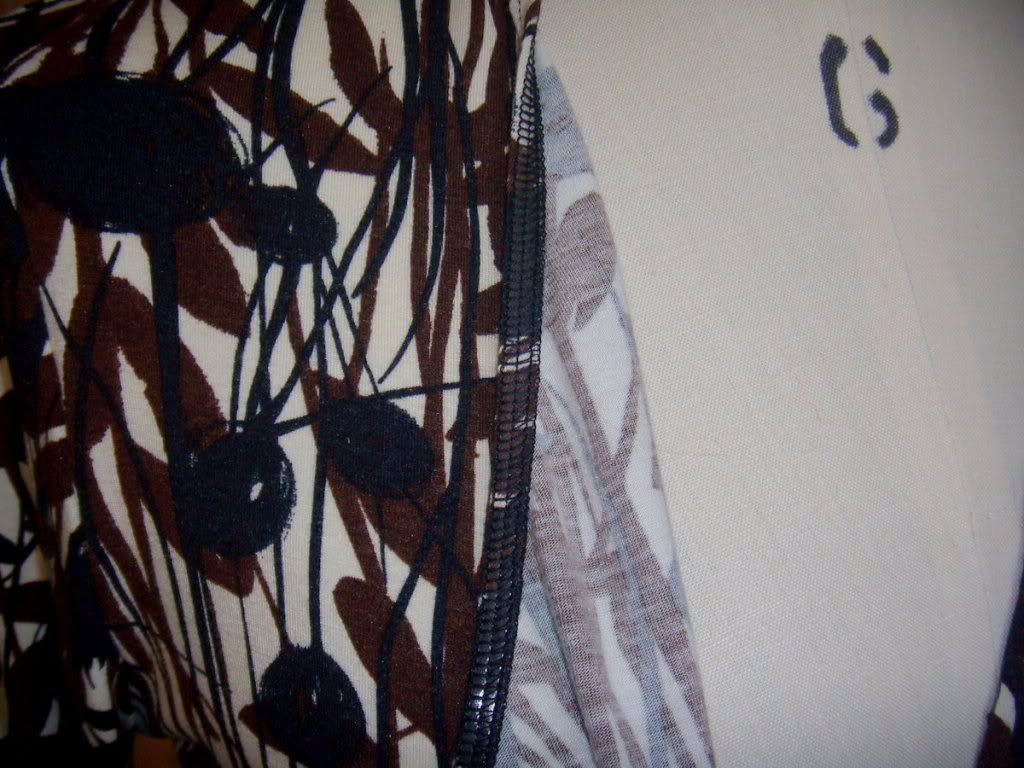
The dress I made for my friend is the same pattern, but I added some fun details: fake pockets, shoulder tabs, and buttons. Look familiar? She liked it so much I found some poly/rayon/lycra doubleknit that would look similar to the wool. She chose silver-tone metal buttons for hers.
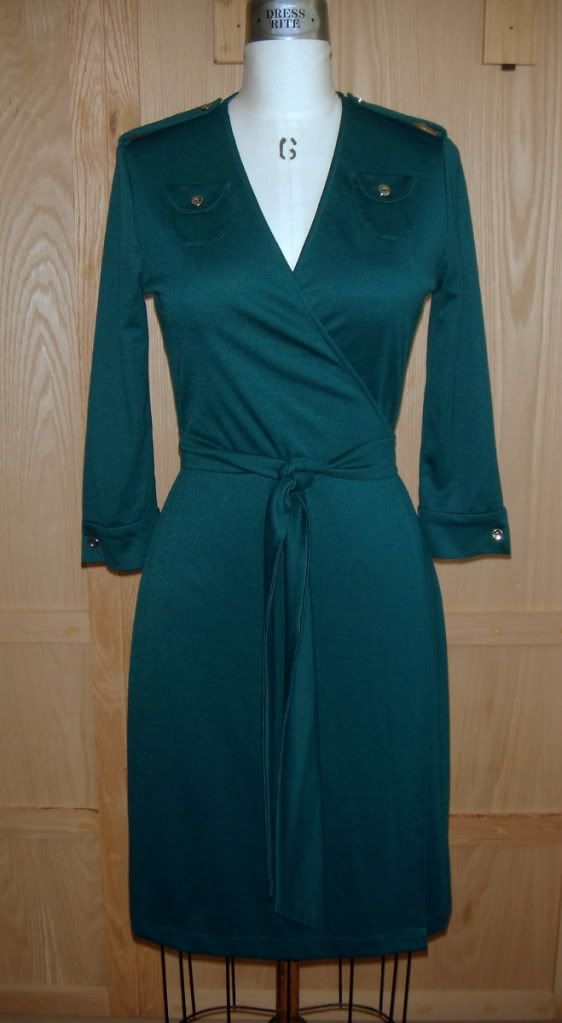
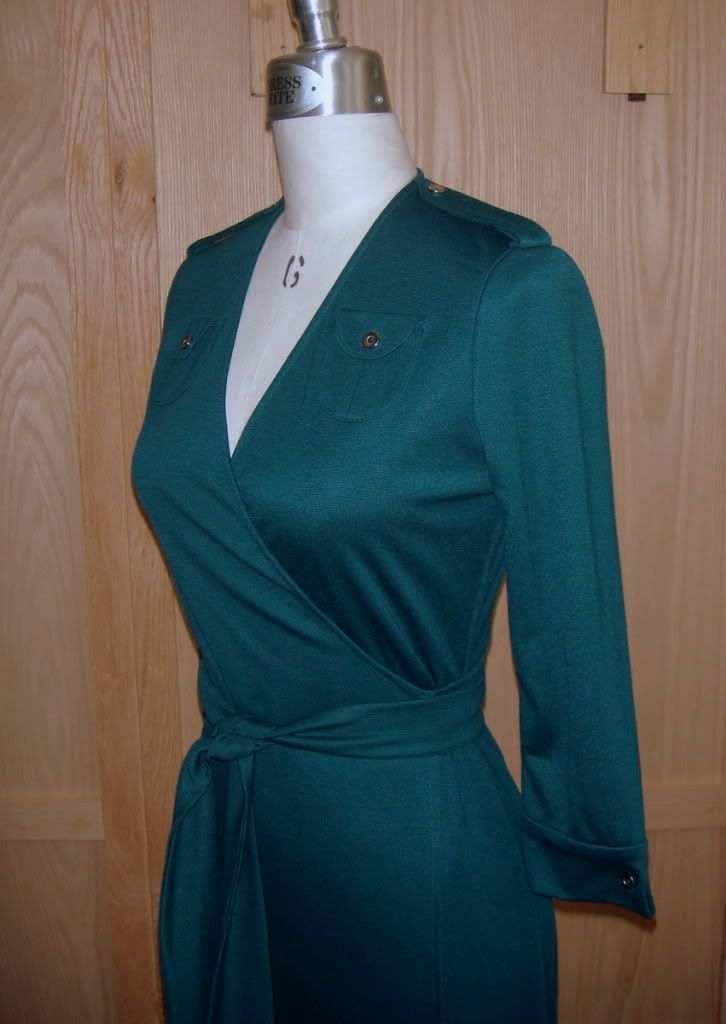
For this fabric, I chose to use double fold binding, as far as I can tell it's exactly what DVF uses to finish the edges of her dresses. It's the same thing as bias binding, except it's done with a clean finish double fold binder for an industrial machine, and you don't preform the fabric. The binder I have takes a 1" strip of fabric, and forms a 1/4" binding. It's designed for light-medium weight fabrics, so when this doubleknit passes through it stretches it a bit, which accomplishes the same thing as stretching the elastic. I use crossgrain strips of fabric, and on the first pass bind the raw edge. Then I turn the whole thing, so the binding is completely on the inside, and topstitch. This edge is very stable and durable.

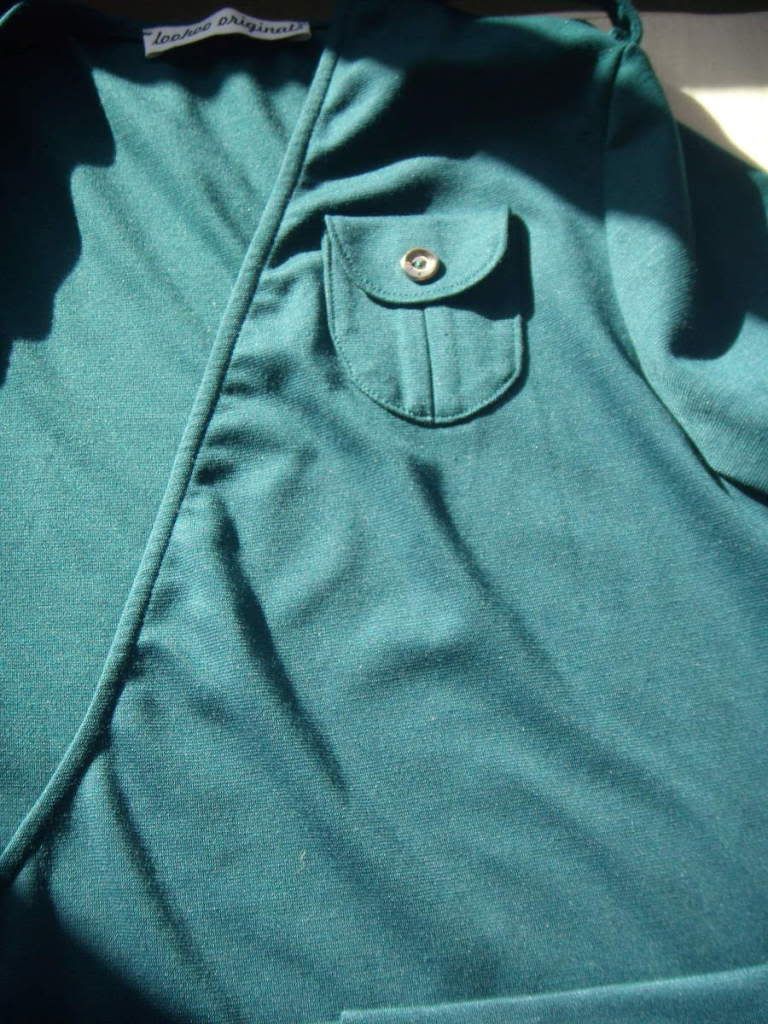
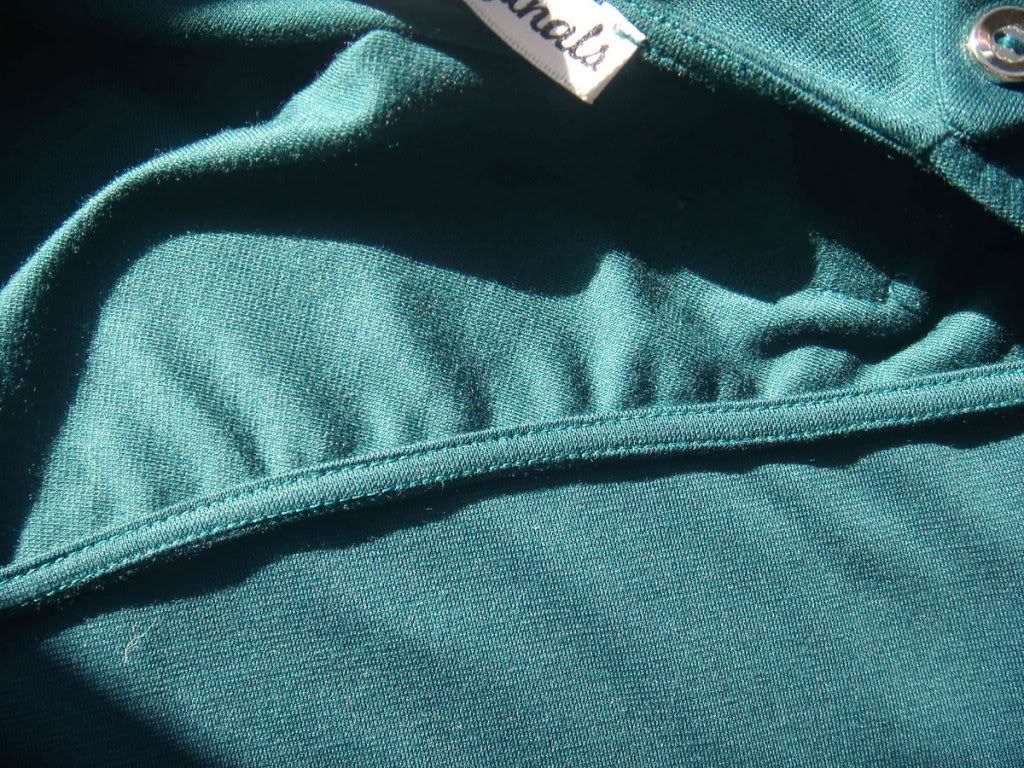