I have been busy collecting new equipment/gadgets in the last month, and as you can imagine playing with them is way more fun than blogging. No offense.
The first piece I need to share is this Elna Alize ironing press. I bought mine from sewinginusa.com, they are one of the few etailers that carries Elna presses. You can't type 'ironing press' into google without hitting a million Simplicity presses, but it took some work to find the Elna. I was looking for a dry press as well, which also made it hard. Most of the presses on the market now come with steam, which means holes in the pressing surface. Tiny holes, but holes. Since I mainly planned on using it for fusing interfacing, I wanted as smooth a surface as possible. The Elna had good reviews on patternreview.com and the price was right, so I went with that.
Features I like:
- 10 second timer that activates when you close the lid. My favorite interfacing needs 20 seconds, so I close the lid twice and I'm done. :-)
- Pressure! Lots of it. (100lbs) I'm convinced this really helps the adhesion of fusibles.
- Heat! Well duh. But it advertises 392F and it definitely gets hot on high.
- Sturdy, it's got locking handles to move it around and rubber feet that don't slide on the table.
- Board is made of Finnish birch, so no warping. At least not yet. (All the other presses use steel mesh). I prefer the way the steam permeates through the fabric with a wood board. The metal mesh on my ironing board isn't the same.
- FUSING AN ENTIRE PIECE OF INTERFACING AT ONCE! (yes you need to get one of these)
- It's 20"x9", and when you are fusing interfacing bigger is better. I can fit two collars, or two cuffs, but not both. it's not long enough for an entire waistband, but it really isn't too hard to move the fabric once part of it is fused. It's still light years better than using an iron. But to go bigger I would have had to get a steam model.
- Not really a big deal, but having to use a spray bottle for steam. I mean you have to spray interfacing or a press cloth anyways when fusing, but when I use it to press shirts or something it does slow you down.
- It came with a spray bottle, which leaked from day 1. I threw it away.
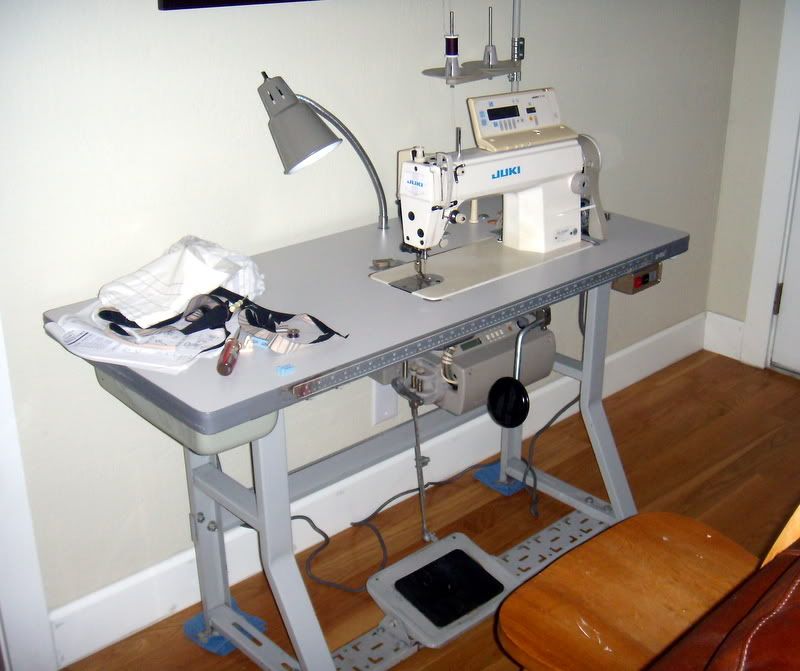
After scouring Craigslist.org for a used industrial sewing machine for several months, I finally found one in San Francisco at the beginning of May for a good price. I've been picking up a lot more 'for hire' sewing projects and the allure of an industrial machine, with all it's capabilites and attachments, was too tempting. It was quite the fiasco picking it up at 6 pm on a Friday night, in the rain, lining up movers to carry it down 3 flights of stairs (one flaked, DH had to stand in. OMG), driving a full-size truck with a utility trailer through downtown SF, and unloading it into the house. Whew! But it's here. And it's awesome. :-)
It's a Juki DDL5550N-7 computerized single needle lockstitch with a servo motor. Features:
- Adjustable speed servo motor, from turtle to rabbit-on-Red-Bull. (holy cow who sews that fast??)
- Auto thread trimmer, activated by depressing the back part of the pedal
- Auto back tacking at beginning or end of a seam (or not at all)
- Reverse
- Knee lifter
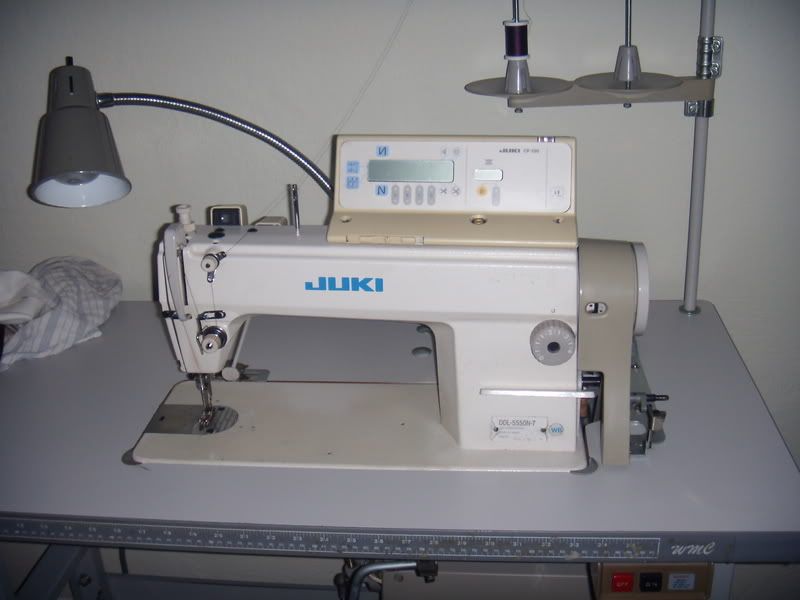

I've only made a couple garments with it so far but the fabric feeding is so much better than my Janome, you can adjust everything (love that), I've decided life before auto thread-trimming sucks, and you can probably buy an attachment that does your laundry and cooks dinner for you. I bought some basic feet (left and right cording, zipper, invisible zipper) and a binder so far and am hooked.
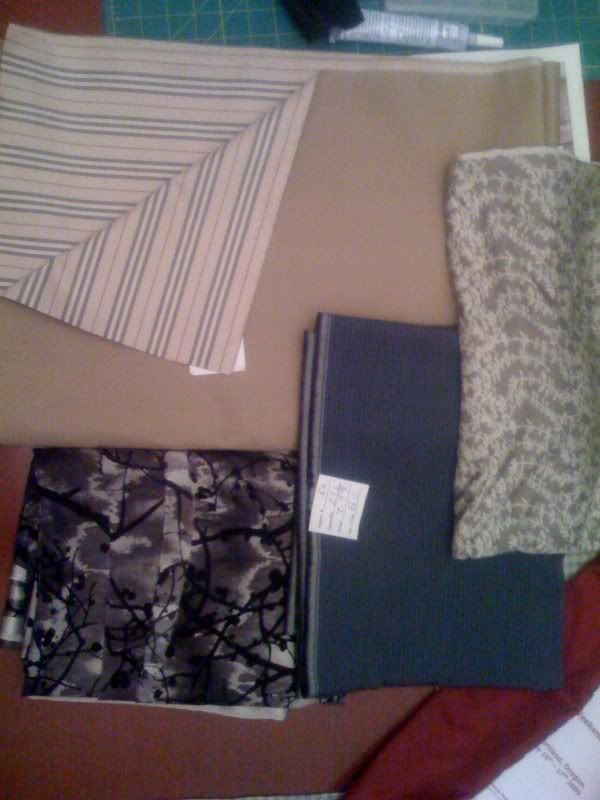
